8 Considerations for Metal-to-Plastic Insertion
Featured Product from Ambrell Induction Heating Solutions
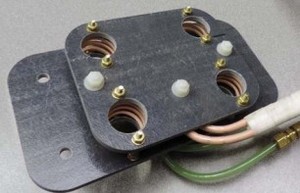
Ambrell Induction Heating Solutions - Metal to plastic insertion -- or heat staking -- is a popular induction application at Ambrell's worldwide application laboratories, also known as THE LAB. Dr. Girish Dahake, Senior Vice President of Global Applications, and his team have seen this application with increasing frequency. He published an article in Industrial Heating on the topic, and here are eight critical parameters that he highlighted for a consistent induction insertion process:
- Tuning frequency: The frequency of operation of the power supply should be chosen to deliver efficient energy based on the size and material of the part. Care must be taken to ensure that this frequency is above the critical frequency of the part for efficient heating.
- Repeatability of the induction power supply: This is the cycle-to-cycle repeatability of the induction power supply in manufacturing given standard incoming voltage variations and other tolerances.
- Heat-on time: This should be the same every cycle to reach the same temperature on the insert.
- Positioning of the insert in the coil: This is dependent on the fixturing and handling device. Varying placement of the insert inside the induction coil will result in inconsistent temperatures of the insert.
- Insertion pressure: The location of the insert in the hole of the plastic part is determined by insert pressure. Lower pressure leaves the insert above the required location, whereas higher insertion pressure may cause undesirable “flash” of the plastic material.
- Fit of the insert in the thermoplastic material: The diameter of the insert hole must be the correct size to allow the plastic to flow around the insert. If the hole is too small, extra plastic will be displaced.
- Cool-down time: Cool down following the insertion cycle is needed to anchor the insert inside the plastic part. If the cool-down time is too short and the insertion pressure is removed quickly, inserts will often be pushed out of the plastic part.
- Insert temperature: The installation temperature of the insert is a key factor in the success of the staking process. Each insert must be heated to the same temperature in the same time to achieve a consistent process.
For more information, visit the Ambrell Heat Staking page, which has numerous application notes along with the full article from Dr. Dahake. Complimentary testing is available from THE LAB at Ambrell, where the applications team will put their decades of induction experience involving thousands of applications to work for you.
More Featured Products