Composite Core Material in Sandwich Panels
Featured Product from General Plastics Manufacturing Co.
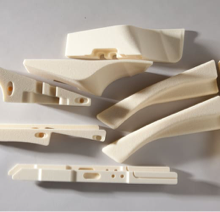
Composite Core: Factors to Consider When Choosing Core Material for Your Application
Composite core materials are used to complete the function of engineered structures by making up for a type of design or performance need, whether it’s weight reduction, providing energy absorption, impact resistance or adding stiffness. It’s important to select the right composite core material that performs as intended and provides the properties specified for your application. However, with so many viable material options available, it’s imperative to first identify the criteria the material needs to meet to help narrow down the decision making process. read more.......
Composite Core Foam Manufacturer
FOR ENDURING PERFORMANCE AT THE CORE, IT PAYS TO START WITH A SUPERIOR PRODUCT.
When you buy composite core foam, it needs to perform as intended and provide the properties specified for your application – in production and over time. That requires a polyurethane foam that is always uniform in density, weight, thickness and cell structure. For absolute consistency and guaranteed performance, General Plastics LAST-A-FOAM® is unrivaled.
With 60 years’ experience in the composites industry, General Plastics understands the exacting standards of OEMs and the importance of rigorous quality assurance. When you select our rigid closed-cell foam products to serve as composite core material, know that they will conform to your specifications at delivery and over time. We also offer fast turnaround and scalability to meet your OEM production requirements.
Not all foams are created equal.
Are the polyurethane foams you’re considering reliably consistent from sheet to sheet, batch to batch, and within each block? Are they easily finished with nearly any resin, paint or coating system? Will they repel water? Bond securely? Prevent the release of toxic fumes or chemical compounds? Do they remain strong, flat and stable – and retain their stated CTE rating – 10 years later?
If a lower-priced foam warps, expands, degrades or resists bonding, it’s far more costly in the long run. Get more for your money by using a superior product in the first place. General Plastics’ anti-static composite foams offer a smooth, grain-free cell structure. The tough material machines beautifully and cuts crisply. These foams retain their strength, dimensional stability and chemical properties for years to come. And, they are free of CFCs and VOCs.
A cost-effective, versatile and long-lasting alternative
Our unique formulations offer a compelling alternative to traditional core materials, such as thermoplastic foam, honeycomb, wood and metal. LAST-A-FOAM® composite core materials have been used for years in the aerospace and automotive industries in place of aluminum, as well as for sports equipment and insulated doors and windows. In the marine industry, General Plastics composite core foams provide a non-decaying alternative to wood that supports fiberglass laminating production processes.
From the impact resistance required for a hockey stick blade to the durability of a wing tip, General Plastics’ LAST-A-FOAM® offers high-strength, low-weight solutions for diverse manufacturing processes. Whether you need board stock or machined parts, we can meet your exacting specifications.
Read this post to learn how General Plastics featured its’ composite core materials for light-weighting applications at JEC World 2018 in Paris, France.
Advantages
- Strong, durable and dependable
- Ideal for the fiberglass-infusion process
- Flame-retardant
- Chemically resistant
- Low resin uptake resulting from fine cell structure
- Various densities available to satisfy both high and low-density applications
Applications
- Resin transfer molding
- Vacuum-assisted resin transfer molding
- Aircraft interior sandwich core panels
- Automotive load floor core panels
- Composite panel cores
- Models and design prototypes
- Vacuum form dies and mold patterns
- Insulated doors and windows
Recommended Products
- FR-3700 Precision Core Series
- FR-3800 FST Aerospace Foam Series
- FR-4300 Thermoformable Board Series
- FR-6700 Aerospace Grade Series
- FR-7100 Multi-Use Core and Modeling Board Series
Use our Product Finder tool to find out what product is suitable for your specific application.
RIGID & FLEXIBLE POLYURETHANE FOAM AND BUILD-TO-PRINT COMPOSITE PARTS
For over 75 years, we have focused on meeting the exacting requirements of engineers and design teams in diverse industries. Our premier LAST-A-FOAM® closed- and open-cell polyurethane foam products provide a high strength-to-weight ratio and extraordinary versatility, with absolute consistency from order to order, guaranteed.
Whether you need high-temperature tooling boards, molded parts or submersible foams, expect identical quality, uniformity, stability and weight for the density you specify – every time.
From the oceans’ depths to deep space, we shape great ideas into reality.