Protecting Linear Rail from Corrosion
Featured Product from Modern Linear Incorporated
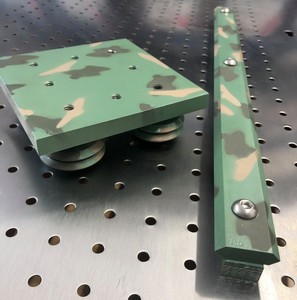
In linear motion applications, protecting rail and track form corrosion is a paramount concern. Keeping the machine system clean and corrosion-free can be a particularly difficult task if the working environment is susceptible to moisture and contamination. When corrosion builds up on the moving components, accuracy and overall performance are diminished and risk of failure increases exponentially. Other linear products such as ball bushings and ball rails use the shaft or rail as the inner race of the bearing, making them susceptible to contamination or corrosion failure. In contaminated environments, these products have to be protected with bellows, or covers, in order to continue working properly. This adds additional component and installation costs. In comparison, v-groove guide rollers excel against corrosion and contamination for a variety of reasons, namely:
- Guide roller radial bearings are sealed/shielded which keeps particular matter and moisture away from the ball path.
- The natural wiping action of the v-edge roller to track interface sweeps away corrosion or contaminate build up.
- Guide rollers offer low cost and ease of installation.
The option to use stainless steel for components is the typical way to deal with the issue of corrosion. We offer 440C stainless steel as an option for our components and track as a standard, stock item. We have also produced 303 stainless track for special applications.
Other cost effective alternatives to full stainless steel material are available as well such as electroless nickel plating, black oxide treatment, and coatings. A low cost option is to simply paint the linear system. The rollers will rub away the paint at the v-edge of the track, but all other supporting surfaces will be protected.
In wet and heavily contaminated environments, visible corrosion can start to appear on the track. While the v-edge is continuously wiped and cleaned by the roller moving back and forth, the rest of the track is exposed. This ‘support’ area is the majority of the surface area, acting as the structural element of the track. In this way, it can be protected from corrosion the same way as the machine frame.
In fact, one of our customer’s was designing a roll out platform to be installed underneath a US Army refueling trailer. Initially, the customer requested completely stainless steel track due to contamination and corrosion concerns after being washed or being transported by sea. Knowing the rollers would clean the v-edge, the conversation went to the structural part of the track. The solution, it turned out, was to treat the structural section the same way the rest of the trailer was done: with military spec camouflage paint. Not only did this prove to be an easy solution to the matter of corrosion, it was also extremely cost effective as well.
In addition to stock components like rollers and track, we have developed several new technologies to handle the issue of corrosion and contamination.
Hybrid Roller Assembly (HRA):
The HRA consists of 3 components; outer tire, radial ball bearing, and inner mounting stud.
The outer tire can be made from 300 or 400 series stainless steel, as well as standard carbon steel. The size and shape can be altered to run on different shapes of track or rail. Ball bearing options range from standard 52100 deep groove ball bearings, to stainless steel, or full complement ceramic bearings. Special lube options are available, as well as no lube. The inner stud is made from 304 stainless steel. The length, size, and shape can be changed to facilitate any mounting configuration.
The assembly is held together with corrosion resistant snap rings allowing for part combinations to be changed easily. Material selections can optimize performance in clean or highly corrosive environments.
The Track Clamp allows the use of two single edge tracks, ensures parallelism for your system, and even enables the track to span a gap. The gaps created between the guide and mounting surface allows debris and moisture to fall away from sensitive components. Using track clamps rather than full length supported guides can also save money without compromising time and cost of installation.