Reaction Injection Molding for Large Parts
Service Detail from Osborne Industries, Inc.
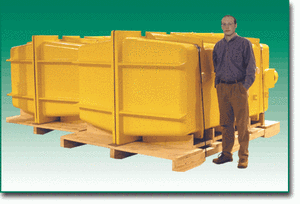
High tooling costs and fast chemical reaction times typically rule out many plastic molding processes when manufacturing very large plastic parts. Osborne Industries has overcome this obstacle in two ways:
First, Osborne Industries can manufacture high quality, composite molds, that can last for many years, making thousands of parts, for a fraction of what a comparable aluminum or nickel-shell plated molds would cost. This is especially important when a part volume is predicted to be relatively low, or unknown.
The second way Osborne Industries addresses cost barriers is by using polydicyclopentadiene (PDCPD) chemistry in a Reaction Injection Molding (RIM) process. Polymer's like Pentam® can be formulated for the production of large parts. These parts can range in thickness from .100-inch - to over 12 Inches and have a surface area ranging from 2ft² to 140ft² or more.
The precise control of reaction chemistry, cure times, additives, and reinforcements means we can meet or exceed the toughest product requirements.
Current OEM applications of this technology include:
- Military Vehicle Fenders
- Chemical Processing tanks
- Agricultural Fenders and Hoods
- Concrete Truck Fenders
- Semi-truck Hoods
The picture shown is a Chlor-Alkali cell cover made by Osborne Industries using Pentam. This material was chosen because of its superior chemical corrosion resistance, durability, and ability be molded into larger parts. It is about 128 ft² in size, weighs almost 1000 lbs, and is about 1" thick.
Osborne Industries has nearly 20 years experience in RIM molding. Please contact us with any questions or about PENTAM®, or any of our thermoset molding processes.