Eng. Ceramics in Steel Production – Sinter Plant
Featured Product from Saint-Gobain Performance Ceramics & Refractories
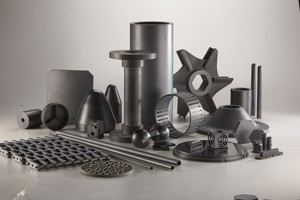
Erosion/Abrasion in Sinter Production
The key processes during sinter production involve homogenizing high throughputs of raw materials, loading, and heating the sinter mix onto the sinter strand, feeding the crystallized sinter cake onto a crash deck, feeding and sizing on the hot screens, and then further cold screening of the sinter before it is sent to the Blast Furnace.
Erosion/Wear - A Sinter Production Nightmare
Wear is omnipresent in the sinter production process, from the sinter mixture preparation to the recycling of fines and sinter transport to the blast furnace. Wear occurs mostly due to abrasion/impact during loading, mixing, material transfer, and thermal stresses during heating. It involves components such as internal linings of bins, sinter mix feed chutes, hoppers, hearth layer, crash decks, hot and cold screen feed chutes, conveyor transfers, dust collection and scrubber.
Portfolio of Wear Resistant Technolgies
Saint Gobain’s high performance wear resistant linings are engineered for efficiently reducing wear in severely demanding applications. Our versatile range of ceramics allows us to supply numerous product specific applications:
- Durafrax® Alumina Materials: the workhorse for wear resistant linings; a high grade, cost effective, extremely fine grained alumina with superior wear resistance against fine particle abrasion.
- Hexoloy® SiC Materials: one of the hardest, high performance wear resistant lining existing. It is a self-bonded, fine grained, and lightweight sintered form of alpha-silicon carbide with excellent sliding wear, corrosion, and thermal shock resistance. It is ideal for high temperature applications with a maximum use temperature of 1900°C.
- Cryston® SiC Materials: a high performance nitride bonded silicon carbide, ideal for chemically harsh environments involving severe wear, erosion, and high operating temperatures. Its maximum use temperature is 1590°C. It can be cast and pressed into complex geometries for challenging refractory applications.
- ZAC-Corguard® is a dense, electrically fused combination of zirconia, alumina, and silica. Its interlocked grains and impervious structure make it an ideal wear resistant solution against heavy impact erosion in crash decks in sinter production.
- Refrax® 20 SiC Materials: a nitride bonded silicon carbide, having a high abrasion resistance and a very low thermal expansion (high thermal stability), with a maximum use temperature of 1590°C.
- Norfrax® RBSiC Materials: a high performance, fine grade reaction bonded (RB) silicon carbide wear resistant material with excellent thermal shock resistance and structural stability, ideal for applications with severe wear. Prepared via sintering, it possesses a high degree of formability, making it ideal for complex lining demands.
- Wearfrax® Monolithics: a class of monolithic castables based on silicon carbide and alumina, having high wear resistance, and impressive ability to withstand thermal shocks, both in low and high temperature applications.
If you would like to speak with one of our experts about using one of these wear resistant linings in your sinter production workflow, simply contact us today.