Thermal Spray Flexicords
Featured Product from Saint-Gobain Coating Solutions
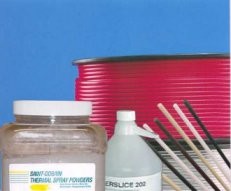
Thermal Spray Flexicords are an alternative to produce metallic and ceramic coatings using a universal flame spray gun. Our Thermal Spray Flexicords are tailored to fit to specific requirements such as: low porosity (down to 3%), high density, low or high roughness, nano sized materials, etc. Versus plasma sprayed coatings, Flexicords offer an excellent performance when coatings are subjected to thermal cycles at high temperatures and they allow a higher coating thickness. The Flexicords are ceramic or metallic wires that are sprayed with a customized flame spray unit (TOP JET or MASTER JET).
Our customers produce coatings that have specific advantages:
• Controlled surface roughness for paper application with further polymer impregnation.
• Very dense, low porosity coatings, low roughness with our range of Alumina-Titania, HardKarb Co12 (WC 12Co) coatings.
• Higher coating thickness of 2 to 3 mm achieved without extra processes.
• Higher thickness coating providing longer life.
• Higher working temperature, that cannot be reached with plasma sprayed coatings.
• Capability to coat on complicated shapes and huge parts.
• Less deterioration of the crystalline structure or stochiometry of the sprayed materials (capability to produce Nano structured Flexicords).
Markets and Applications
Our range of Thermal Spray Flexicords is an alternative to produce metallic and ceramic coatings using a universal flame spray gun for various markets and applications such as metalcasting, glass industry, textile rollers, foundries, paper…. Please see Flexicord for specific product information and data sheets. Applications for Thermal Spray Flexicords are noted below:
Textile
TI-CORDS and SUPRA-CORDS provide hard and very smooth coatings, 2 to 4µm Ra as sprayed.
Applications: textile thread guides, feed separators, pins, rolls, guide bars, sleeves…
Non-Slip coatings
ROCDUR NS, ROCDUR 6740 and HardKarb Co12 (WC 12Co) produce Non-Slip and wear resistant coatings having a roughness higher than Ra 20µm.
Applications: feed rolls, non slip surfaces, non-stick surfaces versus adhesive tapes… Our coatings replace advantageously duplex HVOF coatings and special powder spraying coatings.
Oil & gas, petrochemicals
Ti-Elite, Chrome Carbide, HardKarb Co12 (WC 12Co) and ROKIDE C offer and excellent erosion and wear resistance under corrosion. Our coatings are smooth and can operate under temperatures over 500°C.
Applications: rotor and casing of pumps, pipes, flanges, sleeves, hydraulic valves, ceramic coatings on graphite.
Incinerators & Waste-To-Energy boilers
Our guns are lightweight & versatile, ideal for on site jobs to spray Chrome Carbide, Rocdur 625 and NiCr alloys dedicated to improve the oxidation resistance at high temperature for incinerators and W.T.E boilers.
Applications: boiler water wall tubes, waste incinerators, super heaters, economizers, dust and fume valves…
Aluminum & Zinc metal casting
Our Ceramic Flexicords coatings provide low sticking features versus molten metals. Our coatings have low internal stresses allowing high operating temperatures with thermal cycles (Spinel, Mullite, AZ).
Applications: Spoons, chutes, funnels, moulds…
Steel works and foundries
Compared to plasma sprayed coatings, our ceramic Flexicords provide coatings with less internal stresses, allowing thermal shock resistance and higher operating temperatures (Spinel, Zirconia).
Applications: steel converters, casting chutes, ladles, oxygen lance, coatings on ceramics and graphite.
Glass containers
ROCDUR 40 & 62 provide a narrow spray pattern and improve the deposition efficiency (+50%) versus flame powder. ROCDUR's best performance is proven on narrow parts such as NNPB plungers, ejection pistons, pins of moulds and cavity moulds…
Wire drawing
Our coatings resist to severe friction metal/metal under high pressure during wire drawing. Our guns are versatile and are ideal tools to spray Tungsten Carbide composites, ROCDUR 6740, HardKarb Co12 (WC 12Co), Hard steels and ROKIDE C ceramic coatings.
Repair & Overhaul
Flame spraying allows to rebuild undersized mechanical parts. Flame spraying consists in spraying atomized particles of metal or ceramic onto the part to be repaired. The bond strength of the coating is ranging from 3000 to 8000 PSI.
The advantages of thermal spraying are:
• Fast and economical process
• Range of thickness from 50µm to ~3mm
• No distortion and no heat transfer to the part (max 120°C)
• Coatings can be rebuilt many times,
• Hardness of the coating is ranging from 25 HRC to 75HRC