Flexible UV-Curing Adhesives
Featured Product from Shenzhen DeepMaterial Technologies Co., Ltd
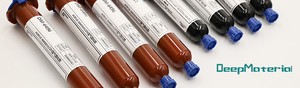
In this blog post, we’ll dive into the world of flexible UV-curing adhesives and explore their benefits, applications, and how to select the suitable adhesive for your industry.
What are flexible UV-curing adhesives?
Professionals use two-part adhesives that consist of a resin and a hardener to create flexible UV-curing adhesives that cure when exposed to UV light. They commonly use these adhesives in applications requiring high adhesion strength and flexibility. They offer excellent bonding properties that allow them to bond with a wide range of substrates, including metals, plastics, and composites.
The curing process of these adhesives is fast and precise, allowing for efficient manufacturing processes. They are also known for their ability to provide a strong and durable bond, even under harsh environmental conditions.
Benefits of flexible UV-curing adhesives
Flexible UV-curing adhesives offer several benefits that make them ideal for various industries. Let’s explore some of these benefits in detail.
Ability to bond dissimilar materials
Flexible UV-curing adhesives have a significant advantage in bonding dissimilar materials. Professionals often consider this feature ideal for connecting multiple substrates in various applications. They can click materials such as metal to plastic, plastic to rubber, and even glass to metal.
This feature reduces the need for additional adhesives and makes manufacturing more efficient.
Flexibility and durability
Professionals prefer flexible UV-curing adhesives for their ability to provide the flexibility and durability needed in many applications. They specifically design these adhesives to withstand stress and movement, making them an ideal choice for applications that involve vibration or movement.
They are also known for their resistance to impact, making them ideal for high-shock load applications. The flexibility and durability of these adhesives make them suitable for industries such as automotive, electronics, and aerospace.
Fast curing times and improved efficiency
Flexible UV-curing adhesives also offer fast curing times, improving production process efficiency. Since they cure upon exposure to UV light, they can be used in automated processes, reducing the need for manual labor and increasing throughput. The curing time can be a few seconds, depending on the adhesive and the intensity of the UV light source.
Fast curing times of UV-curing adhesives can reduce the likelihood of adhesive failure due to movement or misalignment of parts during the bonding process. This feature is essential in electronics and medical devices, where precision and reliability are critical, and fast curing times can improve efficiency.
Resistance to temperature and humidity changes
Flexible UV-curing adhesives can withstand temperature and humidity changes, making them ideal for applications with varying environmental conditions. They can maintain their bond strength and flexibility over a wide temperature range, from -40°C to 150°C, making them suitable for harsh environments.
The automotive, aerospace, and electronics industries require adhesives that can withstand extreme temperatures and humidity, making resistance to these factors essential. By using flexible UV-curing adhesives, manufacturers can ensure that their products maintain performance and reliability over the long term.
Applications of flexible UV-curing adhesives
Flexible UV-curing adhesives have a wide range of applications across various industries. Here are some examples:
Automotive industry
Flexible UV-curing adhesives are commonly used in the automotive industry to bond dissimilar materials, such as plastic and metal, and create seals and gaskets. They can withstand the harsh conditions of engine compartments and provide reliable bonding for critical components.
Electronics industry
The electronics industry uses flexible UV-curing adhesives to bond components like printed circuit boards and displays screens and create seals and gaskets. They offer fast curing times and excellent adhesion strength, which is critical for the reliability and performance of electronic devices.
Medical device industry
The medical device industry uses flexible UV-curing adhesives to bond components and creates seals and gaskets for medical equipment. They offer excellent biocompatibility and can withstand sterilization, making them suitable for various medical applications.
Aerospace industry
Flexible UV-curing adhesives bond components and create seals and gaskets for aircraft and spacecraft in the aerospace industry. They offer excellent resistance to temperature and humidity changes, which is critical for the performance and reliability of aerospace components.