Boosting Performance of Electric Vehicle Wiring
Featured Product from AGC Chemicals Americas, Inc.
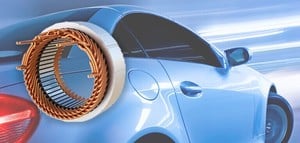
Boosting the Performance of Electric Vehicle Wiring with Fluoropolymer Compounds
Electric vehicle manufacturers are persistently working to develop ways to improve engine performance, raise output density, increase motor efficiency output and make better use of space.
Space utilization is particularly important with wiring. The more wires that can be packed into a space increases the voltage. This is significant because EVs use inverter-drive motors that need to maximize voltage. Today these motors only generate between 200 and 400 volts, but as demand for EVs grows, so does the desire for more voltage. The next-generation motors will likely generate 800 volts.
Within a motor stator, rounded wires achieve a 78-88 percent occupancy. Because more flat wires can fit into the space, they can reach 96 percent occupancy. New fluoropolymer compounds for flat wire jackets enable automakers to move away from traditional rounded wires.
How can different wire jackets improve EV performance?
Higher voltage demands, governmental requirements and environmental regulations are driving the need for new EV materials. This includes wire jackets.
Existing wire jacketing materials have limitations when it comes to EVs. For example, when polyimide (PI) and polyamide-imide (PAI) are used as the enamel layer, the material is too thick to provide sufficient reliability for high voltage. Pinhole defects can also occur when using PI and PAI.
When polyetheretherketone (PEEK) and polyphenylene sulfide (PPS) are used as the polymer layer in extrusion processes, adhesion is poor. Also the material has inadequate flexibility and is susceptible to cracking.
With these inadequate jacket materials, the insulating film deteriorates when the inverter surge invades the winding wires and parts. Discharge occurs, and the motor can no longer withstand high voltages.
Why are fluoropolymer compounds a better choice for wire jacketing?
Fluoropolymer compounds are exceptionally suitable for wire and cable coatings thanks to their excellent electrical and insulating properties. They work effectively in a wide range of temperatures, and are able to withstand heat and harsh chemicals.
In fact, you can use fluoropolymers as polymer and enamel layers for flat wire coating materials. Fluoropolymers provide excellent electrical and insulating properties in a wide range of temperatures. They also provide heat and chemical resistance. These materials provide improved performance in critical cable constructions when they replace neat PEEK, thermoset PI and perfluoroalkoxy alkane (PFA).
Why are fluoropolymer compounds more versatile than other materials?
You can use these new fluoropolymer compounds in both dispersion/powder and extrusion coatings. They improve the performance of both the polymer and enamel layer to insulate high-voltage wires. Besides adhering better to Cu/PI, they provide better flexibility, electrical insulation and cost savings.
When compared with existing PI enamel coatings, new fluoropolymer adhesive products show stronger adhesion to Cu/PI when used in dispersion/powder processing. They also provide better electrical insulation. As noted above, PI alone is not reliable and is prone to pinholes.
Adhesive PFA can be used by itself or combined with PI because it adheres well to both materials. Adhesive PFA adheres much better to PI and Cu than PFA, with no loss in PFA performance. Our researchers demonstrated these results with a 90° peel test.
For extrusion coating, PFA-based adhesive compounds adhere better to many materials when compared with neat PI and PEEK. Neat PI is not reliable enough for high voltage, and pinhole defects occur. PEEK adheres poorly to PI, is not flexible enough, and cracks when bent.
PFA- and PEEK-based fluoropolymer compounds are a better choice for the polymer layer. They adhere strongly to copper, PI, thermosetting resins, thermoplastic resins and glass. They also resist cracking, are flexible and provide the same insulation properties as neat PFA. PFA- and PEEK-based fluoropolymer coatings provide improved electrical insulation when they are applied via liquid/dip process.
What fluoropolymer compounds does AGC offer for flat wire jackets?
Our Fluon+™ materials are based on fluoropolymers and demonstrate improved insulation properties when compared to existing wire jacket materials.
- Fluon+ adhesive PFA EA-2000 fluoropolymer coating is ideal for thin insulation applied via liquid/dip process for improved electrical insulation.
- Fluon+ PFA-based materials are applied via extrusion process for improved conductor adhesion, crack resistance and flexibility.
- Fluon+ PEEK-based materials are applied via extrusion process for improved conductor adhesion, impact strength and better abrasion loss.
Follow us on:
Watch>>>AGC Group Overview
ABOUT AGC CHEMICALS AMERICAS
For almost a century, AGC Chemicals has been manufacturing high-performance materials serving industrial customers. Already the world's largest, longstanding custom compounder of PTFE and other fluoropolymer resins, AGC continues to build its product line with the introduction of FFKM resins that meet the growing demand for tougher, more durable products for today's production and manufacturing environments.