Choosing the right potting compound why it matters
Featured Product from ELANTAS PDG, Inc.
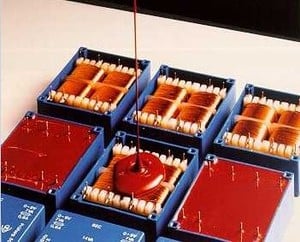
Potting compounds seal and protect electrical components from various stresses, chemical exposure, moisture and other environmental elements that can damage or shorten the lifespan of the device. The potting compounds themselves are polymeric and cast from a liquid state to fill around the electrical component.
The challenge lies in choosing the proper potting compound chemistry. For the engineering device manufacturer, developing the specialized chemistry that meets all of the necessary design requirements and is easily castable can be difficult. Instead, it is advantageous to partner with an industry expert like ELANTAS PDG, Inc.
Design challenges with potting compound chemistry
At first glance, it may seem simple enough to develop a “one-size-fits-all” potting compound for all applications. However, this approach can lead to failed products in the field, disappointed customers and larger expenses in the long run. The specific application should be used to determine the design requirements, and ultimately the chemical composition of the potting compound.
Chemical composition has an impact on flowability during casting, thermal properties, bonding to components, physical properties and ultraviolet and chemical exposure. Certain chemistries work well in specific applications but not all. For example, mass produced components that utilize room temperature curing materials will save on energy costs. This same potting compound would not be a good choice for sensors used in aerospace applications that require higher operating temperatures.
The chemistry of a potting compound also impacts electrical properties, such as dielectric constant, frequency response, resistance or impedance, breakdown voltage and others. A potting compound used to protect the contacts of a small switch will be different than those used to protect the windings of a large transformer.
What makes a good potting compound?
The full scale design of a potting compound must take into account all of the application and industrial requirements. These requirements form the basis for evaluating whether a potting compound will perform as needed.
Electrical properties
The ideal potting compound for a specific application will have the proper dielectric constant, electrical resistance and breakdown voltage. If the dielectric constant is wrong, the capacitance will change, which thus changes the electrical resistance, dissipation factor, power factor and frequency response of the circuit. If the breakdown voltage is too low, current will pass through the potting compound instead of through the circuit components. In order to ensure proper operation, the potting compound must have predictable electrical properties.
Thermal stability and properties
Potting compounds must maintain thermal stability across their entire expected temperature range. Most people mistakenly think of thermal stability only in terms of glass transition temperature. However, polymers will age in different ways with time and temperatures. Polymers will oxidize and become more rigid, and they can undergo weight loss where low molecular weight species are released over time.
Besides the lifetime of the component, thermal stability can also impact how a material behaves electrically. Higher temperatures lower the resistivity of the material and also impact dielectric constant and dissipation factor.
Finally, thermal properties also must be tailored to strike the balance between a material that will remain functional at all required temperatures, yet easily cast into shape. The casting process requires the material to flow easily enough to backfill all space in the electrical component. Heating above this temperature represents wasted energy.
Heat dissipation
Another challenge related to thermal properties is the ability of a potting compound to remove heat from the device. Unfortunately, polymers are notoriously poor at allowing heat to flow through them. In relays, transformers and other high current devices, the buildup of heat can lead to an increased fire risk or damage to the component. Air is the worst thermal transfer medium. Using a potting material improves heat flow. Adding inorganic materials or fillers to the polymer can also be beneficial. However, this will compromise other characteristics such as liquid flow. By choosing the right chemistry for the application, heat can be dissipated in a safe and efficient manner.
Adhesion
Potting compounds rely on adhering to all of the necessary pieces of an electrical component. An application might include materials such as plastic sensor housings, stainless steel sensor bodies and copper windings. To provide protection, the potting compound must flow around and secure all parts, as well as fill in any voidspace to prevent the buildup of moisture, mold, fungus or other contaminants that will drastically reduce the usability of the device.
Industries served
The potting compounds developed by ELANTAS have been successfully deployed in many industries. In particular, the power distribution, automotive, marine, consumer goods, wire wound product markets and other industrial applications where electromagnetic devices are found, have benefited from optimized potting compounds.
Power distribution
In the power distribution industry, transformers are typically oil-filled or casted with potting compounds. The oil-filled transformers are heavier and can leak, thus leading to a fire risk, so there is a major advantage to the use of cast resin transformers. The key is to tailor the potting compound chemistry to meet the demands of an outdoor installation, as moisture, mechanical damage and other threats can shorten the life of the potting compound.
Automotive and marine
Figure 2. It is imperative that potting compounds withstand harsh and temperamental applications like automotive ignition coils to avoid overheating. Source: ELANTAS
Internal combustion engines use ignition coils that light the gasoline. Due to the high temperatures and potentially corrosive environment, the two internal coils must be sealed with a potting compound. This potting compound must protect the coils from mechanical damage, thermal damage, moisture, chemical attack and have the proper dielectric constant to ensure that the spark is directed toward the fuel rather than arcing to other components.
Wire wound products
Electric motors, transformers, electromagnets, inductors and many other electrical devices rely on wound wire. Transformers, for example, have several large inductors made from wire wound around a laminated metal core. One of the biggest failure modes of transformers is damage to the wire wound around the core. A properly designed potting compound can be used to secure the wound wire, preventing movement and extending the life of the transformer, while also transferring heat away from the coils during operation.
ELANTAS advantage
ELANTAS develops custom chemistry solutions for the electrical and electronics industries. Because each product has different engineering needs, ELANTAS works to understand the specific design requirements to determine the best chemical formulation for the job.
While there are a handful of companies that produce potting compounds, ELANTAS provides unmatched application support. They work with the product designers throughout the whole process to ensure that the potting compound will meet all the design requirements, as well as provide product support during the casting, troubleshooting and other operations required for bringing final products to market.
Developing a potting compound can be far too time-consuming to be economical. Rather than attempting to develop and test potting compounds in house, it is cost-effective and time-efficient to partner with ELANTAS. Contact ELANTAS today and let their team of chemists and technical experts develop the right custom potting compound for your application.