Coating thickness of PVD-coated tools Using XRF
Featured Product from Fischer Technology, Inc.
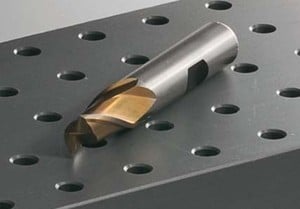
As with all types of coatings, the PVD process must also be closely monitored and the thickness of the PVD-deposited layer measured. Alongside standard destructive testing methods, the non-destructive X-ray fluorescence method (XRF) is preferable for this purpose.
High-precision industrial saws, drills and dies used for the cutting, punching and forming of steel, hard metal or aluminum parts are subject to extreme wear and tear. To increase the service life of these often very expensive tools, they are coated with a hard material coating via a PVD (physical vapor deposition) process. The thickness of the PVD layer determines the durability and therefore the life expectancy of the tool.
As with all types of coatings, the PVD process must also be closely monitored and the thickness of the PVD-deposited layer measured. Alongside standard destructive testing methods, the non-destructive X-ray fluorescence method (XRF) is preferable for this purpose. Measurement of the coating thickness of hard material coatings such as TiN, TiCN, CrN or CrVN using the X-ray fluorescence (XRF) measuring instruments FISCHERSCOPE® X-RAY XDAL® and XDV®-SDD.
The instrument’s specialization for this purpose means that layer thickness can be accurately measured on even the finest cutting edges of very high-end tools. Furthermore, using the same instrument, it is possible to determine the base tools’ precise metallic composition – e.g. to determine Cobalt leaching when an old coating is chemically removed before a new coating is applied.
For additional information or to learn more about Fischer Technology’s line of X-ray fluorescence instrumentation visit www.fischer-technology.com or call 860-683-0781.