The Most Common Metal Coatings and Finishes
Service Detail from Protomatic, Inc.
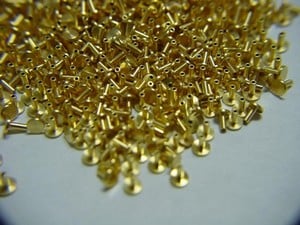
Anodize ASTM-A-8625
Anodizing is great for corrosion control, cosmetic color and surface hardening. The most common anodizing process is the Type II. Note that aluminum alloys with copper, silicon and magnesium do create color variations from alloy to alloy and batch to batch.erties that can protect or optimize product performance; many reference a military specification; and most are processed by NADCAP suppliers
Chemical Film Mil-DTL-5541
Conductive coating for aluminum. Color options are clear and yellow. Available in hexavalent chromium free.
- Class 1a - Maximum corrosion protection, typically used for painted applications.
- Class 3 - Low electrical resistance on the surface enables dissipation of static electricity.
Zinc QQ-Z-325
Zinc plating is the go-to process for rust protection of steel parts for most commercial applications, it is available in thickness and treatment type, clear and yellow dichromate and phosphate being the most common.
Black Chrome Mil-C-14538
Provides chrome corrosion protection, with a dark appearance.
- Flash and Hard Chrome
This is a thin, dense chrome that is hard (Rc78) and was developed to provide protection against corrosion and wear. Some processes are proprietary and trademarked such as Armology TDC.
- Show Chrome
Automotive chrome for show or museum quality. Used for part restoration, with a highly polished surface.