How Different Loads Impact Motor Selection
Featured Product from Portescap
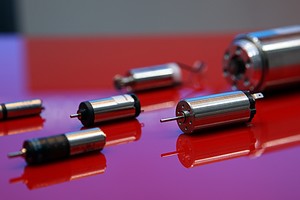
Motor selection involves balancing many considerations, such as the application’s required voltage, maximum current and diameter, speed and efficiency. That’s because different types of loads will have a significant impact on the required motor design, as well as on its lifetime and reliability. Selecting the most appropriate motor for your application requires attention to the fundamentals of torque, radial and axial loads. Here are some tips and best practices for addressing these loads.
Torque Loads
A motor converts electrical energy (Pelec = voltage x current) into mechanical energy (Pmech = torque x rotational velocity). Simply selecting a motor based on the required torque value “x” is usually insufficient. The required torque and velocity in an application must be understood over the entire motion cycle because the motor needs to provide the necessary mechanical power without overheating.
Radial Loads
Bearing options will depend on radial loading. For a brush DC or stepper motor, sleeve bearings are low cost and typically support a lower radial load and provide less lifetime. Sometimes using two sleeve bearings instead of ball bearings can significantly reduce expenses. However, when a radial load is present, use at least one ball bearing for the front bearing of the motor, which helps to ensure a good lifetime.
In contrast, brushless DC motors typically use two ball bearings and can be driven at much higher speeds. A motor manufacturer will recommend the maximum radial dynamic force to achieve a motor’s minimum lifetime at a desired speed.
Dynamic Axial Loads
If an application requires a 90-degree rotation of the rotating movement at a lower speed, a worm gear can be ideal. The worm shaft drives the worm wheel with a reduction ratio as small as ~2:1 or larger. The motor must support the load as it follows the spiral thread on the worm shaft.
When supporting significant axial loads, ball bearings are often mandatory. The maximum recommended dynamic axial load of a motor will depend on the ball bearings and preload used, the distance between the two ball bearings in the motor, and the lifetime requirement.
In a typical axial brushless DC motor design, the dynamic axial load is supported by the front ball bearing. If an axial push load acts on the motor, the preload on the front ball bearing is reduced, causing additional radial play that impacts motor lifetime. With an axial pull load, the load acts in the same direction as the internal preload and increases its stress.
Static Axial Loads
A static axial load may be applied to the shaft either during shock loads, or when an additional component is press-fitted onto the motor shaft of the assembled motor.
If a motor is equipped with ball bearings, a press-fit operation’s recommended limit is typically much higher than for a dynamic axial load. As long as the static load applied to the bearing is below its elastic limit, there will be no permanent deformation of the bearing balls or raceway. Similarly, exceeding the maximum recommended load can cause the bearing balls and raceway to deform, thereby reducing its life. Also, consider whether the rear shaft of the motor can be supported during press-fitting. This allows for a higher force by sending it through the motor shaft instead of the bearings.
Collaboration With Your Motor Provider Is Vital
It’s important to consider torque, radial and axial loads in relation to their impact on a motor and the motor selection process. A dedicated motion solution provider — like Portescap — can support you in calculating the loads experienced by a motor. And, we’re fully equipped to develop the most suitable motion system to fulfill your application requirements.
For more information, visit www.portescap.com or read the full whitepaper here.