Small DC Motors Power High-Traction Sewer Robots
Featured Product from FAULHABER MICROMO
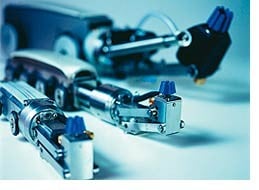
Thousands of miles of underground pipes are responsible for handling important tasks. They have to operate reliably. Internal inspection and maintenance has so far only been possible where pipe diameters are large. Relatively small sewers do not offer enough space for human beings, and whenever they were damaged the only solution was to expose the affected pipe sections. An expensive undertaking. However, new developments in the field of electronics and motion control engineering now make it possible to inspect and perform maintenance in small sewers - internally. Since in the sewage sector all tools have to meet very high standards of reliability and performance, the drives on such sewer robots have to be extremely robust. Modern bell-type armature DC motors satisfy the exacting requirements for use inside of the pipe system.
The large and extensive sewage networks operated by local authorities and companies, which are often quite old, require regular maintenance. In an increasing number of cases there is minor and major damage to be repaired. For such work on the pipe system PROKASRO, a sewer robot specialist, developed an extensive range of tools and equipment. From an autonomous service vehicle (fig. 1) with auxiliary equipment such as a generator, compressor, water tank, and electronic control the robot is steered using a cable remote control and a monitor.
Sewer robots have various sizes, tooling, and other specific features depending on the type of service (fig. 2). What they all have in common is supply and control via a supply cable. The cable is comprised of 32 electric wires, four compressed air hoses and four water hoses. The robot drags this trailing "umbilical cord", which is 39 mm thick, behind it through the sewer. The standard length is 120 m but it is also possible to reach lengths of up to 200 m. At that length and with the amount of dirt that always occurs in the sewer a powerful drive is absolutely vital for smooth operation.
The problem was solved by using miniature DC motors incorporating a coreless rotor - made by FAULHABER.
For example, one version of the robot is equipped with nine motors of this type in order to allow flexible operation under ground. The drive used consists of four axes each comprised of one Series 3557...CR motor. The motor is coupled to a gearhead in order to be able to ensure optimal adjustment of speed and traction.
The advantage of this solution is that the same robot can work in large pipes with large wheels; appropriately stepped-down gears reduce the rotary speed in proportion to wheel size. Velocity and traction are thus kept independent of wheel diameter; the operator at the service vehicle can work as accustomed. A secure stance is provided by a pneumatic cylinder that presses the upper pairs of wheels against the inside of the pipe. Even slight damage like cracks or dents in the pipe are easily negotiated by the rubber-tired wheels. Despite their small size, the combined traction of the four drive motors is around 1,000 N (in other words 100 kg).
In order to examine and work on each part of the pipe interior, the front of the robot is provided with a swiveling camera and an air-powered milling machine. Here, too, the motions are driven by miniature DC motors. Another motor mounted between the wheel drives allows the robot head to rotate around its longitudinal axis.
Inside of the head itself there is a DC motor in the tilting device of the milling machine (fig. ).
Two small motors allow camera panning and control the focusing mechanism (fig. ).
The chief advantage of FAULHABER drives in this case is their high power density, making the robot so small that it can be deployed from a pipe diameter of 200 mm upward. However, it is also suitable for pipe sizes up to 600 mm.
Being low-voltage motors with a voltage supply of less than 42 V, they satisfy the requirements for underwater operation. The high level of efficiency maintains the waste heat inside of the enclosed housing, which is kept at positive pressure with compressed air, within reasonable limits. An essential aspect is also the direct response to control commands. Movement on the monitor image and movement of the robot have to be virtually synchronized and delays due to motor ramps must be minimal. That is the only way in which the operator can move the robot reliably inside of the pipe having undergone only a short period of familiarization.
Nowadays, sewer robots with state-of-the-art camera electronics and drive components reduce the cost of inspection, maintenance, and repairs to underground sewer networks. Optimally configured, extremely small drive solutions are the key component to enable flexible activities even in narrow pipes. The reliability of miniature DC motors and their high level of efficiency permit extremely compact