Metalworking Lubricants, Coolants, and Fluids Information
Metalworking lubricants, coolants, and fluids are used for metal forming, metal cutting, lapping, polishing, and grinding applications. They lubricate, decrease thermal deformation, and flush away removed material. The use of metal working fluids also improves surface finishes and increases tool life.
Metalworking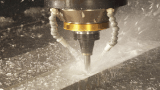
Metalworking is any process used to shape, form, cut, or machine a metal workpiece. Metalworking lubricants, coolants, and fluids are specialized coatings and carriers for metal forming, metal cutting, lapping, polishing, and grinding applications.
-
Metal forming is a process used to plastically deform a workpiece. In order to achieve the desired shape or geometry, a force must be applied that exceeds the material's yield strength. Metal forming oils, greases, and fluids dissipate heat, lubricate the working surface, and prevent localized strain that would otherwise cause damaging effects both to the tool and finished product.
-
Metal cutting is a machining operation used to remove material and dissect workpieces. The primary function of the cutting fluid differs dependent on the cutting speed. At low speed the fluid acts as a lubricant prevent galling, friction welds, or other friction-induced wear at the cutting surface. At high speeds the fluid primarily acts as a coolant, preventing thermal deformation. Cutting fluids also function to remove cuttings, inhibit corrosion, and improve the cutting surface finish.
-
Lapping, polishing, and grinding are metalworking operations used to improve the surface of a workpiece. In lapping or polishing compounds, fluids or oils are used to carry abrasive powders. In grinding applications the main function of metal working lubricants, coolants, and fluids is to perform workpiece cooling.
Functional Uses
Metalworking fluids (MWFs) reduce or eliminate thermal deformation, localized strain, inhibit corrosion, and flush away removed material.
Thermal deformation is a phenomenon experienced in machining operations due to the combing effects of plastic strain and friction-induced heat at the tool and workpiece interface. The increased temperature gives rise to surface toughness, increased thermal error in precision machining operations, and decreased tool life. Cutting fluids counter these problems by lowering the coefficient of friction and transferring heat away via convection, thereby increasing the temperature gradient at the machining interface.
The following formula illustrates how heat is generated at the tool interface by friction:
Where:
Ic = Intensity of Friction Heat Source
F = Friction Force
Vx = Sliding Velocity
h = Plastic Contact Length
b = Cutting Width
Localized strain occurs when there is a break-down in the lubrication regime. Localized areas that experience undesired solid-to-solid contact experience a spike in friction. This may cause the material to undergo some amount of strain, damaging either the tool or workpiece. Metalworking fluids (MWFs) are carefully designed to effectively lubricate the workpiece by anticipating the temperature and pressure environment that they experience in a given metal forming operation.
Corrosion is a natural process where the surface of a substance, typically a metal, deteriorates due to a reaction that occurs within its environment. A corrosion inhibitor is added in small concentrations to the environment in order to control the rate or eliminate corrosion. In MWFs they are added to protect the untreated, exposed surface formed during the machining operation. To learn more about corrosion inhibitors please visit IHS's learn more page for rust preventives and corrosion inhibitors.
Types
Metalworking lubricants, coolants, and fluids include various types of fluids used in metalworking operations that are illustrated by the following table:
Electrical Discharge Machining (EDM) Fluids |
EDM fluids are dielectric fluids that provide specific voltage and amperage characteristics in EDM operations. They serve two functions, to stabilize a fixed spark gap ionization potential and to remove eroded debris. |
Flood or Mist Coolants |
Flood or mist coolants are heat transfer fluids used to dissipate heat that is generated at the tool chip interface. They allow for heavier cuts, faster cutting speeds, and improved surface finishes in almost all machining operations. |
Grinding Fluids |
Grinding fluids are coolants that may also include extreme pressure or chemically-active additives. They are used to improve and protect surface finishes and may also be used to disperse abrasive powders. |
Metal Cutting Fluids |
Metal cutting fluids are used in metal machining to improve tool life (reduce wear), increase lubrication, reduce workpiece thermal deformation, improve surface finish, and flush away chips from the cutting zone. |
Metal Forming Fluids |
Metal forming oils, greases, and fluids are designed to enhance lubrication during extrusion, wire drawing, stamping, bending, swaging, rolling, embossing, and other deformation processes. |
Mold releases and release agents are film-forming lubricating oils, solid lubricants, waxes, fluids, or coatings that prevent other materials from sticking or adhering to an underlying surface. | |
Quenching oils and heat treatment fluids provide rapid or controlled cooling of metallic parts. They are used to temper, harden, or treat the material to achieve desired physical properties. |
Product Form
There are three basic product forms of MWFs: fluids, greases, and solid lubricants or dry film lubricants.
-
Fluids are water-based liquids, oils, or fluids supplied in liquid form.
-
Greases, gels, and lubricating pastes are thick, high viscosity products that do not run or flow off surfaces. Greases often consist of oil thickened with a sodium or calcium soap complex or non-soap thickener.
-
Solid lubricants or dry film lubricants are compounds such as hexagonal flake graphite, boron nitride (BN), molybdenum disulfide, or polytetrafluoroethylene (PTFE) powders.
Composition
Metalworking lubricants, coolants, and fluids vary widely in terms of chemical composition. They may be classified as being either petroleum or mineral oil-based, or synthetic or semi-synthetic.
Petroleum or mineral oils
Petroleum and mineral oil products are functional fluids derived from petroleum. They include a broad range of hydrocarbon-based substances of varying chemical compositions and a wide variety of physical properties. Specific constituents present include aromatic, naphthenic, and paraffinic fluids.
Synthetic or semi-synthetic
Synthetic or semi-synthetic fluids include fluids with a base of glycol or polyglycol, ester or diester, or silicone-based fluids. They exhibit outstanding thermal and dielectric properties. The characteristics, cost, and heat transfer performance of semi-synthetic fluids fall between those of synthetic and soluble oil fluids.
Other Specialized Fluids
Other specialized fluids include high water content fluids (HWCF), lithium complexes, aluminum complexes, waxes such as paraffin and stearate, and halogenated hydrocarbons including chlorofluorocarbon (CFC), halogenated fluorocarbon (HFC), halogenated chlorofluorocarbon (HCFC), and perfluorocarbon (PFC).
Performance Specifications
Important properties for metalworking lubricants, coolants, and fluids include concentration, flash point, and autogenous ignition temperature (AIT).
-
Concentration is measured after dilution of the fluid solution on a volumetric basis.
-
Flash point is the lowest temperature at which a liquid can give off sufficient vapors to form an ignitable mixture in air near the surface of the liquid.
-
Autogenous ignition temperature (AIT) is the temperature at which ignition occurs spontaneously.
Standards
ASTM D2881 - This classification covers and is designed to standardize and consolidate the terminology, nomenclature, and classification of metalworking fluids and related materials.
ASTM D6482 - This test method covers the equipment and the procedure for evaluation of quenching characteristics of a quenching fluid by cooling rate determination.
ASTM E2275 - This practice addresses the evaluation of the relative inherent bio-resistance of water-miscible metalworking fluids, the bio-resistance attributable to augmentation with antimicrobial pesticides, or both. It replaces Methods D3946 and E686.
Resources
A Tutorial on Cutting Fluids on Machining
Introduction to Heat in Machining
Image Credit:
CIMCOOL | Fabricating & Metalworking | 3M Electronics Design & Manufacturing
- Alabama
- Arkansas
- Arizona
- California
- Colorado
- Connecticut
- Florida
- Georgia
- Iowa
- Illinois
- Indiana
- Louisiana
- Massachusetts
- Maryland
- Michigan
- Minnesota
- Missouri
- North Carolina
- New Hampshire
- New Jersey
- Nevada
- New York
- Ohio
- Oklahoma
- Pennsylvania
- South Carolina
- Tennessee
- Texas
- Utah
- Virginia
- Washington
- Wisconsin
- West Virginia
- Aerosol / Spray
- Aerospace
- Automotive / Transportation
- Biodegradable
- Coolant (Flood / Mist)
- Dielectric / EDM
- EP (Extreme Pressure / Active)
- Ester / Diester
- Graphite
- Grease
- Grinding Fluid
- Low / Non-foaming
- Lubricant
- MIL-SPEC / Military
- Metal Cutting
- Metal Forming
- Micro-dispersion
- Molybdenum / Metal Sulphide
- Natural (Vegetable Oil / Animal Fat)
- Petroleum / Mineral Oil
- Quenchant / Heat Treat
- Rust / Corrosion Preventative
- Silicone
- Solid Lubricant / Dry Film
- Specialty
- Chemistry / Constituents: Specialty / Other
- Specialty / Other
- Synthetic / Semi-synthetic
- Water Soluble / Emulsion
- cutting oil
- drilling fluid
- thermal oil
- lapping oil
- lapping fluid
- AIT
- coolant spray
- cutting lubricant
- mist coolant
- machining coolant
- metal forming lubricant
- metalworking fluid
- seal barrier fluid
- drawing compound
- drilling lubricant
- grinding fluid
- mist lubrication
- rolling mill oil
- viscosity of fluid
- aerospace coolant
- ASTM fluids
- barrier fluid
- copper alloy cutting fluid
- diester fluids
- drawing lubricant
- drill grease
- flood coolant
- fluid power equipment
- grinding coolant
- grinding grease